Wie door de enorme werkplaats bij het hoofdkantoor van Van Mossel in Waalwijk loopt, kan zich verbazen over de procesmatige inrichting. Alleen de indeling van de ruimte voor schadeherstel roept vraagtekens op.
De ruimte waar het schadeherstel wordt uitgevoerd, is ruim en overzichtelijk. Aan één kant van de ruimte zijn vier lanen met elk ruimte voor drie auto’s in de lengterichting. De lanen worden gescheiden door lage muren. Dit lijkt een vreemde opstelling, want de middelste auto in de laan kan nergens heen zonder dat de auto voor of achter hem weggereden wordt. Waar de rest van de werkplaats uitblinkt in flexibiliteit, lijkt deze opstelling juist erg rigide.
Uiteraard is er wel degelijk goed nagedacht over deze indeling. De opstelling van drie auto’s achter elkaar in een laan past helemaal in de procesmatige manier waarop de hele werkplaats is ingedeeld. Om te begrijpen hoe dit in elkaar zit, moet je begrijpen wat voor rol deze werkplaats vervuld binnen Van Mossel, en wat voor auto’s hier komen om gerepareerd te worden.
Fleet hub
“Op deze locatie richten we ons op het afleveren van nieuwe auto’s en de remarketing van occasions en auto’s die uit onze eigen lease komen”, aldus Ad van Diepenbeek, directeur Schade. “Het is een fleet hub, die bedoeld is om lokale vestigingen te ontzien. Het concept van de fleet hub werkt alleen bij een bepaald volume. Daarom zijn de werkzaamheden op verregaande wijze gestandaardiseerd.”
Nieuwe auto’s worden in Waalwijk klaar gemaakt voor aflevering. Veel hoeft hier meestal niet aan te gebeuren. Het gaat hierbij vaak om grotere aantallen, zoals vlootafleveringen. Deze auto’s komen doorgaans niet op de schade-afdeling. Het zijn vooral de auto’s voor remarketing die hier komen. Deze auto’s komen uit de lease, vaak uit de eigen leasevloot van Van Mossel. Ze worden hier klaargemaakt voor de verkoop.
In de door Explora en Brekupa ingerichte werkplaats wordt standaard onderhoud uitgevoerd. Denk hierbij aan het vervangen van vloeistoffen en slijtdelen, maar ook andere kleine werkzaamheden zoals simpele programmeertaken en het monteren van een trekhaak. Voordat het echter zover is, zijn de auto’s uitgebreid schoongemaakt in de eigen wasstraat. Hierna gaan ze naar speciale ruimtes met veel verlichting. Medewerkers inspecteren hier elke auto op schades. Uiteraard moeten alle schades gerepareerd zijn, voor de auto in de verkoop gaat. Zodra een schade wordt geconstateerd, gaat de auto het schadeproces in.
Niet ingewikkeld
Het aantal auto’s dat via de werkplaats in Waalwijk gaat, is erg hoog. Jaarlijks zijn dit 45.000 auto’s. Soms arriveren er wel 1100 auto’s in één week. Het is de bedoeling dat elke auto binnen vijf dagen de locatie weer verlaat om aan zijn nieuwe leven te beginnen. Ongeveer een vierde van deze auto’s gaat via de schade-afdeling. Dat zijn dus 350 auto’s per week met kleine of grotere schades, die gerepareerd moeten worden.
Hier komen de drie elementen voor standaardisatie samen: grote en constante volumes, vaak hetzelfde soort auto’s en eenvoudige schades.
Het gaat hier echter niet om ingewikkelde schades. Als een auto grote schade heeft, of als er merk-specifieke kennis nodig is, dan komt deze auto niet in deze werkplaats in Waalwijk. Deze schades worden gerepareerd bij andere vestigingen van Van Mossel, waar men meer kennis heeft van het desbetreffende merk of over meer specialistische kennis beschikt.
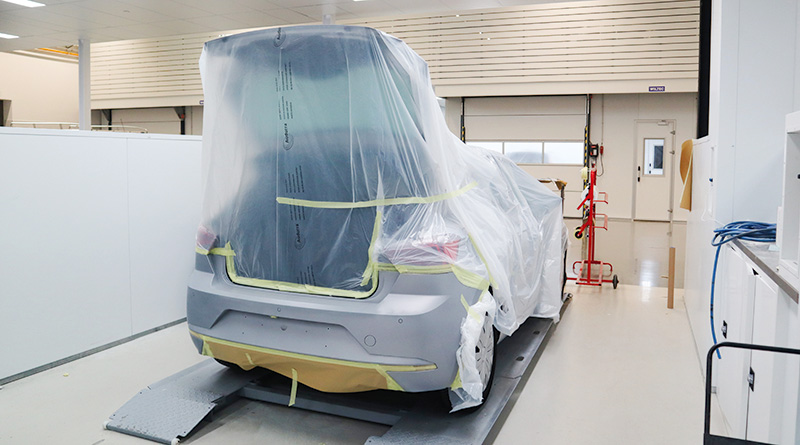
Bij Van Mossel in Waalwijk komen alleen auto’s met kleinere en eenvoudigere schades. Denk aan kleine deukjes of lakschades. Hier komen dus de drie elementen voor standaardisatie samen: grote en constante volumes, vaak hetzelfde soort auto’s en eenvoudige schades. Dit is het recept voor een standaardproces, oftewel schade-afhandeling in de vorm van een lopende band.
Procesmatig
De vier lanen bij de schade-afdeling hebben elk plaats voor drie auto’s. De auto’s die gerepareerd moeten worden, lopen de hele laan door. Op de eerste positie worden beschadigde onderdelen gedemonteerd. Nieuwe onderdelen worden op de auto gezet op de tweede positie. Ten slotte wordt de auto op de laatste positie geprepareerd voor het spuiten. Aan het einde van de laan is de Wiltec spuitcabine. Elke laan heeft zijn eigen cabine, zodat auto’s uit verschillende lanen nooit op elkaar hoeven te wachten.

Omdat het hier om eenvoudige werkzaamheden gaat, duurt het proces op elke positie ongeveer even lang. De auto’s bewegen dan op een gelijke snelheid door de laan en zitten elkaar hierbij nauwelijks in de weg. De medewerkers die hier werken, hebben hun eigen vaste werkplek en gereedschappen. Daadwerkelijk als een lopende band dus. Op deze manier heeft Van Mossel het proces van schadeherstel een stuk efficiënter gemaakt.
Uiteraard werkt dit alleen bij volumewerk. Als er sprake zou zijn van ingewikkelde schades, high-tech onderdelen of noodzaak voor specialistische kennis zou dit systeem van vier gescheiden lanen met drie posities juist belemmerend werken. De auto’s zouden elkaar constant in de weg staan, waarbij de ene moet wachten tot de andere weg is. Door echter goed na te denken over de positie van fleet hub in Waalwijk heeft men het proces zo gestandaardiseerd en gestroomlijnd, dat Van Mossel hier optimaal profiteert van schaalvoordelen. Zelfs als het er op de eerste oogopslag wat vreemd uitziet.
Foto boven: Elke laan heeft zijn eigen cabine, zodat auto’s uit verschillende lanen nooit op elkaar hoeven te wachten.