Jezelf opnieuw uitvinden is complex. Toen Bosch Transmission Technology in Tilburg zich realiseerde dat de vraag naar duwbanden ging afnemen, begreep het wat te doen. Met enthousiasme transformeerde de fabriek in Bosch Thin Metal Technologies.
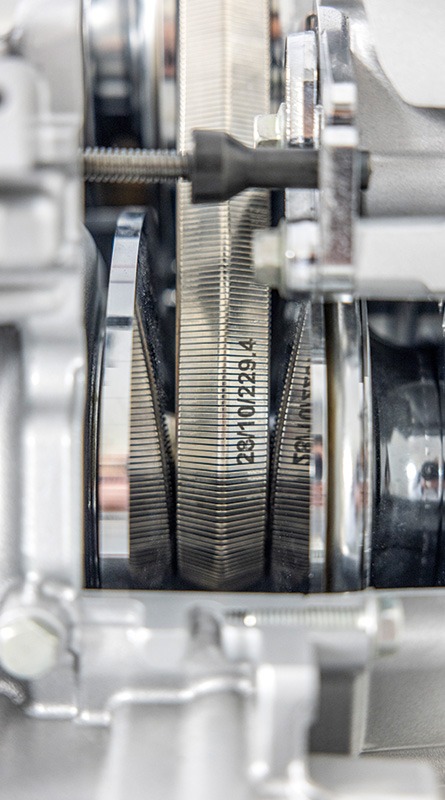
Weinigen realiseren zich hoe belangrijk de uitvinding is van de DAF Variomatic. Het pientere pookje leidde tot een revolutie in de autowereld. Hoewel vaak bespot, is de continu variabele transmissie, oftewel CVT, niet meer weg te denken. Eén van de belangrijkste onderdelen van deze traploze automaat is de duwband: de band die beweegt over twee schijven van wisselende grootte.
Voor de productie van de toen nog rubberen duwband werd in Tilburg in 1972 een fabriek geopend. Halverwege jaren tachtig schakelde Van Doorne Transmissies, zoals het toen heette, over op metalen duwbanden. Deze waren sterker, maar niet eenvoudig te produceren. Om de duwbanden sterk en toch flexibel te maken, was heel specifieke kennis nodig. Dit werd de specialisatie van de fabriek in Tilburg.
De CVT groeide in populariteit en Van Doorne Transmissies werd te klein voor de globale automarkt. Met de overname in 1995 was Bosch Transmission Technology geboren. Daardoor kon de fabriek in Tilburg uitgroeien tot een wereldwijde leverancier van duwbanden. Onlangs rolde de honderdmiljoenste duwband van de productielijn in Tilburg. Naar schatting is wereldwijd elke vierde automatische transmissie een CVT. In de meeste hiervan zit een duwband van Bosch Transmission Technology, geproduceerd in Tilburg of in de zusterfabriek in Vietnam.
‘Duwband nu onderdeel van iets overkoepelends’
Duurzame technologieën
Hoewel de CVT nog steeds populair is, neemt het totale volume af. Elektrische auto’s hebben meestal geen meertrapstransmissie. In Tilburg besloot men niet af te wachten. De kennis moest ingezet worden op een nieuwe manier om naast duwbanden andere onderdelen te gaan produceren.
“Binnen een decennium zijn we ineens vier nieuwe producten gaan maken. Twee hiervan zijn ondertussen al in productie”, vertelt Han-Hein Spit, vicepresident van Bosch Thin Metal Technologies. Onder deze naam worden de nieuwe producten gemaakt. Bosch besloot zijn kennis van hoogwaardige metaalbewerking in te zetten voor nieuwe duurzame technologieën.
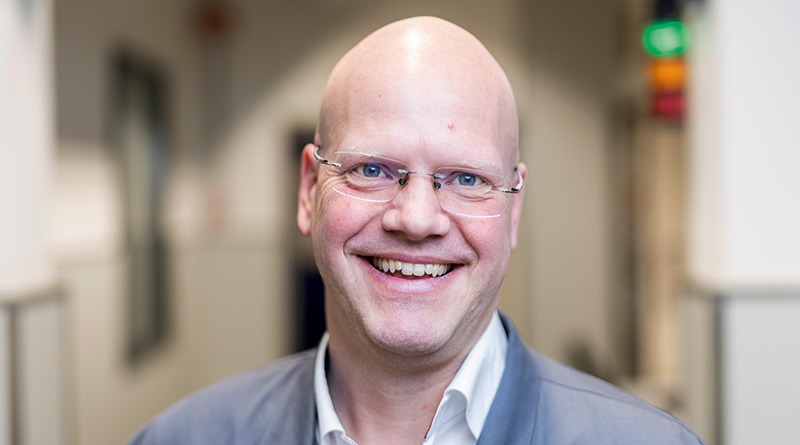
De basis van de productie bij Bosch in Tilburg is metaalbewerking. Met de productie van duwbanden heeft men unieke kennis opgedaan met het vormen en stansen van metaal, lassen en precisie-assemblage. Producten kunnen worden geproduceerd met een precisie tot een duizendste millimeter. Daarnaast is expertise ontwikkeld op het gebied van ontwikkeling en massaproductie. “Wij koppelen complexe productietechnieken aan massaproductie. Hierdoor kunnen wij hier metalen componenten maken die eigenlijk niet geschikt zijn voor massaproductie”, legt Spit uit. “Hierin zijn we uniek in de wereld.”
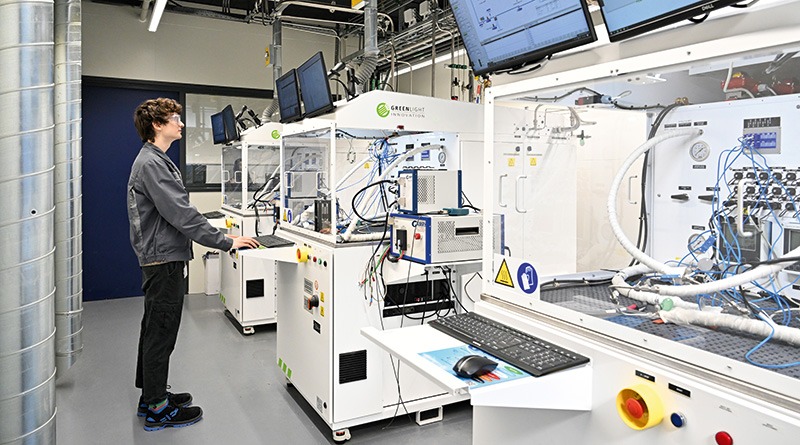
Complexe producten
Naast de productie van duwbanden is Bosch eind vorig jaar gestart met de productie van e-stacks en luchtlagers. Ook dit zijn extreem dunne metalen onderdelen die met bijbehorende precisie gemaakt moeten worden. E-stacks zijn dunne metalen platen, geoptimaliseerd voor elektrische geleiding en magnetische velden. Ze worden opgestapeld tot een stator en een rotor, de twee componenten van een elektromotor. De e-stacks van Bosch worden op een unieke manier gemaakt. Hierdoor hebben ze product- en materiaaleigenschappen die niet haalbaar zijn met normale productiemethoden. Niet alleen biedt dit meer flexibiliteit in het ontwerp, maar ze kunnen ook hogere vermogens leveren. Bovendien gaan ze efficiënter met energie om.
De luchtlagers van Bosch zijn nog complexer en een innovatief alternatief voor de traditionele lagers die iedereen kent. De smeringloze luchtlagers zijn uitermate geschikt voor toepassingen die gevoelig zijn voor vervuiling en corrosie. Bovendien kunnen ze zeer hoge draaisnelheden aan. Dit maakt ze perfect voor bijvoorbeeld luchtcompressoren in brandstofcellen. De productie van luchtlagers is extreem complex: tot nu toe kon niemand dit in massaproductie. Sinds vorig jaar maakt Bosch ze in Tilburg. Eerst voor eigen toepassingen, maar ondertussen is er ook interesse van buitenaf.
Grens van het maakbare
Op vrij korte termijn wil Bosch Thin Metal Technologies ook platen gaan maken voor elektrolyser stacks en brandstofcellen. Dit zijn dunne metalen platen met extreem dunne groeven, die nodig zijn om water om te zetten in waterstof in elektrolysers. Ook bij het omgekeerde proces, in een brandstofcel, zijn dergelijke platen nodig. Bosch gelooft in een brede toepassing van deze waterstoftechniek: niet alleen voor motoren van auto’s en vrachtwagens, maar bijvoorbeeld ook bij energiecentrales van de toekomst. “Het gaat veel verder dan duurzame mobiliteit”, verzekert Spit. “Dit is echt groot.”
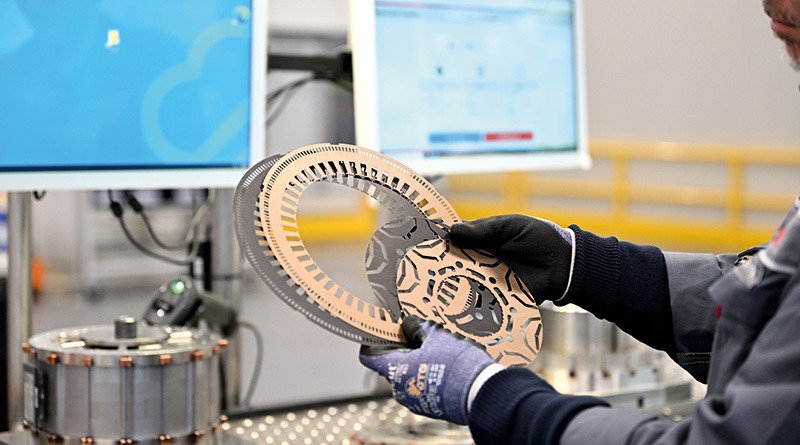
Op dit moment wordt gekeken hoe de elektrolyser-platen het beste geproduceerd kunnen worden. In Tilburg worden ze niet alleen door middel van simulaties in de computer getest, maar ook in een speciale container op het terrein. Deze ontwikkeling is binnen Bosch niet onopgemerkt gebleven. Dankzij zijn engineers is de fabriek in Tilburg door Bosch aangewezen als ontwikkelcentrum van de complete elektrolyser-business. “Binnen tien jaar zijn we hier onderdeel geworden van de waterstoftechnologie”, aldus Spit.
“Onze specifieke kennis en vaardigheden om hoogwaardige oplossingen op de grens van het maakbare te ontwikkelen en te produceren worden nu ingezet om de problemen van deze tijd aan te pakken”, gaat hij verder. “We leveren hightech metalen componenten voor toepassingen in elektromobiliteit en waterstoftechnologie. Ik ben bijzonder trots dat we met Tilburg deze weg kunnen inslaan en kijk vol vertrouwen naar een duurzame toekomst van ons bedrijf.”
Kantelpunt
De overgang naar de nieuwe producten betekent niet het einde voor de duwband. De productie hiervan bij Bosch Transmission Technology gaat gewoon door. De Thin Metal Technologies komt er gewoon naast. Waarschijnlijk komt rond 2030 het kantelpunt. Dan neemt de interesse in de duwband af en breken de nieuwe technieken door, verwacht Bosch.
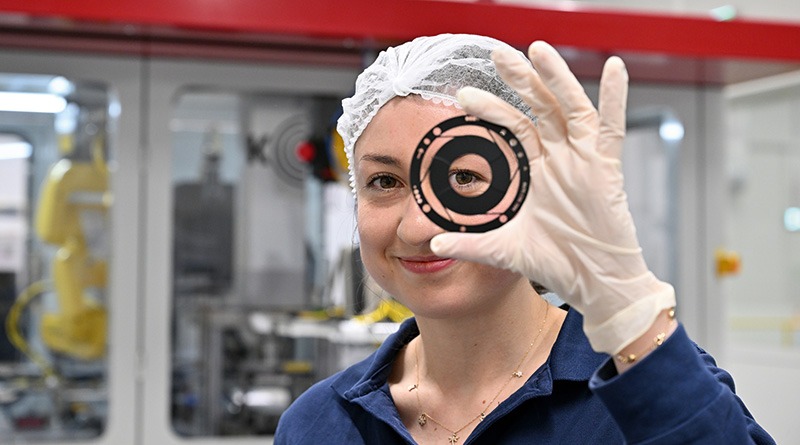
Spit roemt het enthousiasme waarmee zijn medewerkers de uitdaging hebben opgepakt. “Groeien en afbouwen gebeurde hier naast elkaar. Het was voor ons belangrijk dat iedereen enthousiast bleef. Dat is goed gelukt.” Het proces was echter niet zonder uitdagingen. Vorig jaar gingen nog een aantal arbeidsplaatsen verloren bij Bosch. “Dat was heel pijnlijk en vervelend, maar gelukkig was er veel begrip”, vertelt Spit.
Tegelijkertijd werden ook nieuwe medewerkers aangetrokken, experts op andere gebieden. “Wij weten alles over transmissies, maar niet over elektrische motoren of waterstof”, legt Spit uit. “De duwband is nu een onderdeel van iets overkoepelends. Het was een hele uitdaging, maar het is ons goed gelukt.”