Toen Andreas Mayer zo’n twintig jaar geleden bij Bosch begon, werd hem voorgehouden dat het onnodig was je te verdiepen in trommelremmen. Twintig jaar later spelen die juist een rol in de voorbereiding op Euro 7. Aftersales Magazine kijkt achter de schermen op zijn thuisbasis in Karlsruhe.
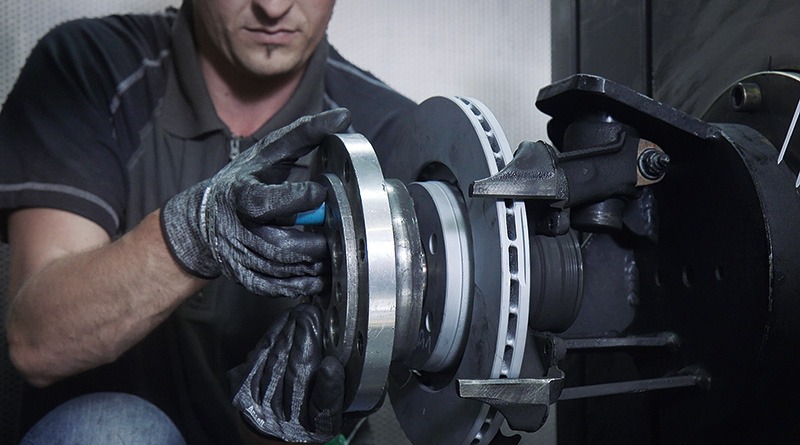
Het is dik een halve eeuw geleden dat de huidige locatie in Karlsruhe in gebruik werd genomen. Met de automotive heeft het allemaal nog weinig te maken, in 1971 worden er prefab woningen geproduceerd door de joint venture Strukturbau Bosch-Wüstenrot. Zeven jaar later krijgt het de bestemming die het nog altijd heeft: logistiek centrum voor aftermarket auto-onderdelen. Op dat moment kan men nog niet bevroeden dat het anno 2024 het hart vormt binnen het wereldwijde distributienetwerk van Bosch.
Het huidige distributiecentrum telt 83.000 m2 aan opslagruimte en 135.000 palletplaatsen plus 230.000 plekken voor de opslag van kleinere onderdelen. Die voorraad arriveert dankzij ongeveer zeventig vrachtwagens die de goederen van 230 fabrieken en toeleveranciers bezorgen. Ook de uitgaande stroom verloopt weer via circa zeventig vrachtwagenladingen naar 6000 verzendadressen. Voor de goede orde: dat zijn niet de autobedrijven, maar de distributeurs zoals LKQ/Fource, Alliance, Motorparts en Doyen. Enkele grote grossiers krijgen indien gewenst rechtstreeks beleverd. Zo’n 300 mensen werken er in drie dagelijkse diensten.
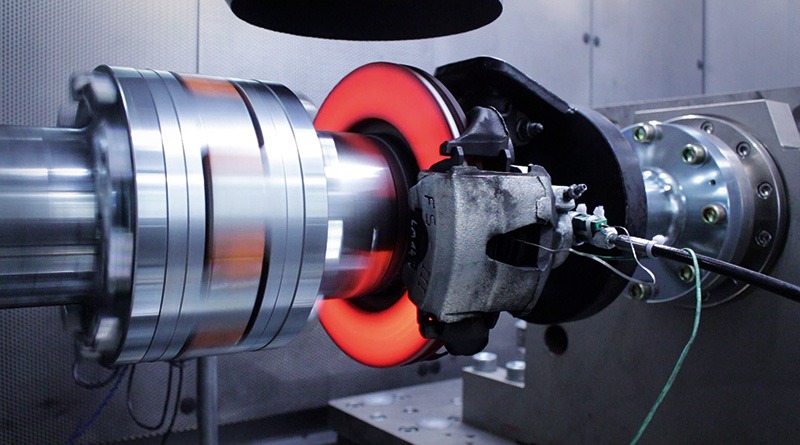
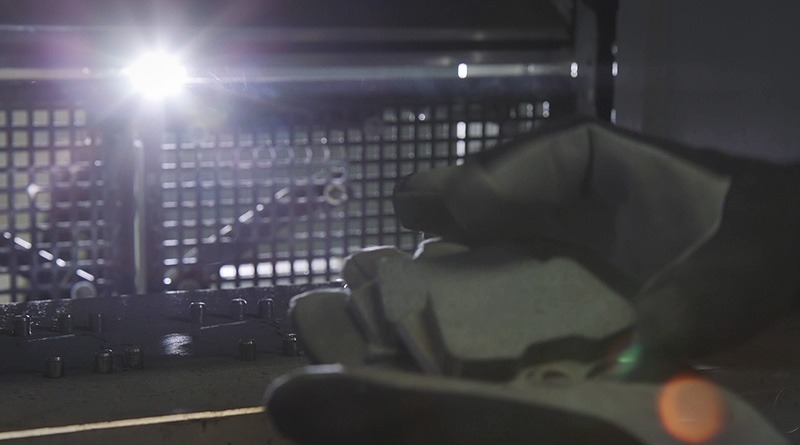
Mobility Aftermarket
Al met al liggen er hier in Karlsruhe zo’n 70.000 artikelnummers die vallen onder de Bosch Mobility Aftermarket-divisie. In Karlsruhe werkt tien procent van het totale Bosch Mobility Aftermarket-personeelsbestand: 1600 mensen. Wie bij het lezen van die divisienaam even de directe herkenning mist, dat kan kloppen. Het is de nieuwe naam voor wat we kenden als Bosch Automotive Aftermarket: de nieuwe naam past niet alleen beter bij het huidige tijdsbeeld, maar omvat bovendien voorheen overlappende divisies. In Karlsruhe zijn overigens nog zes divisies te gast, maar voor Mobility Aftermarket is het het hoofdkwartier.
Hoe interessant de rondleiding door het in hoge mate geautomatiseerde distributiecentrum ook is, het kan niet op tegen de kans rond te kijken in de testlaboratoria waar de aftermarket-remmen worden ontwikkeld. Vanaf komend jaar komt ook de productontwikkeling met testlaboratoria voor starters en dynamo’s naar Karlsruhe.
Bijna 100
De historie van de Bosch automotive remtechniek gaat ver terug, bijna honderd jaar inmiddels. Niet alleen komt het bedrijf in 1927 met het fenomeen rembekrachtiging, maar in 1936 patenteert het bovendien al een anti-blokkeersysteem. Vorig jaar vierde Bosch nog dat ABS al 45 jaar in productie is. Voor zowel ABS als ESP claimt het bedrijf de wereldwijde nummer één te zijn.
We vinden de Bosch-producten niet alleen als eerste montage terug, maar ook in de aftermarket en dat is vandaag de focus tijdens ons bezoek. Andreas Mayer benadrukt dat de complexiteit die zichtbaar is aan de kant van de eerste montage zoveel mogelijk moet worden beperkt voor de aftermarket. “Zodra productie van het voertuig eindigt, treedt een nieuwe fase in werking. Een beperkt aantal artikelnummers moet een zo breed mogelijk pallet aan voertuigtypes bedienen. Dat betekent dat er gezocht wordt naar specificatiecombinaties waardoor een artikelnummer op zo veel mogelijk types past en wel steeds de benodigde prestaties levert.”
Receptuur
In het lab waar twaalf man werken worden verschillende taken uitgevoerd. De inkomende grondstoffen worden allereerst getest. Het zijn natuurproducten en die zijn aan natuurlijke verandering onderhevig. Dat vraagt om controle. Remvoering zoals we dat kennen is terug te voeren op een variëteit aan grondstoffen.
In zo’n tien jaar tijd draaide de verhouding tussen ingekochte en zelf ontwikkelde producten binnen de remdivisie honderdtachtig graden van 70/30 naar 20/80 nu.
In het recept zitten rubbers en vezels, maar bijvoorbeeld ook hout. “Hout verbrandt en dat zorgt voor hele kleine gaatjes in het materiaal wat ons helpt bij het behalen van de compressienormen. Blokken mogen een samendrukbaarheid van maximaal twee procent hebben maar daar blijf je normaal gesproken ver onder.” Koper is als bestanddeel sinds enige tijd aanwezig op de lijst met verboden middelen voor remmen in de VS en in Europa kiest men er daarom voor het ook niet meer toe te passen. “Om die eigenschappen te compenseren hebben we een wat uitgebreidere mix nodig dan voorheen.”
In het lab worden de prototypen geproduceerd, zo zien we de kisten met de namen Passat, C-klasse en die van andere testvoertuigen erop. Concentreren we ons eerst even op de remblokken dan zien we dat de remvoering en de geperste achterplaat één geheel zijn, maar tijdens het productieproces doorlopen de twee elementen eerst een afzonderlijk pad. De geperste achterplaten krijgen na een zandstraalbeurt een lijmcoating. De remvoering wordt hier bij een temperatuur van 140-170 graden hydraulisch op geperst waarna het geheel in de oven gaat. Met zaken als de klemmetjes gemonteerd en de verse laklaag is het remblok klaar.
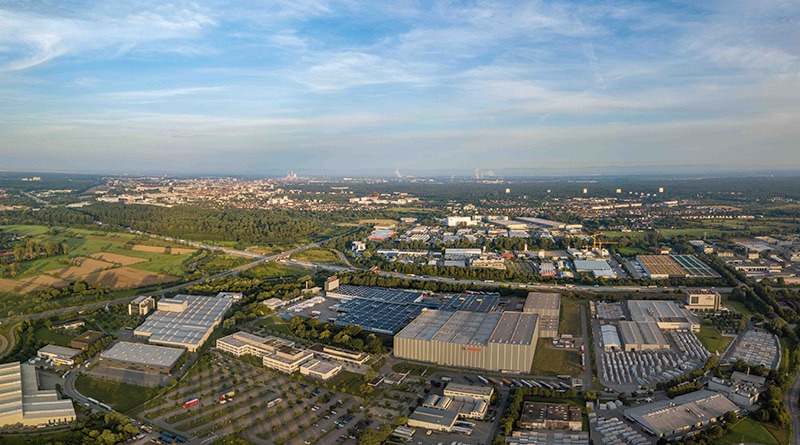
Berglandschap
De prototypes ondergaan elders in het lab verschillende testprocedures. Zo wordt er gekeken wanneer het remblok van de achterplaat komt. We krijgen een voorbeeld te zien waarbij de achterplaat een klein berglandschap heeft van restanten remblok. “Het laatste wat je wilt zien is dat de achterplaat schoon is want dan was er dus geen onderlinge hechting. De normen binnen de ECE-R90 dicteren dat de hechting tussen achterplaat en remblok niet mag falen. Als het remblok bij extreme krachten alsnog loskomt dan is dat een breuk in het remblok zelf. Die krachten meten we hier om zeker te zijn dat we voldoen aan de gestelde eisen.”
Behalve de compressietest en de zogenoemde shear test waarbij die remblokbreuk wordt geforceerd staan er ook enkele dynometers. Daarmee kan het remsysteem, zoals bijvoorbeeld schijf en blokken, onder gecontroleerde omstandigheden op gesimuleerde routes getest worden. Een voorbehoud geldt daarbij wel: het camber (de hoek ten opzichte van de gesimuleerde weg) verandert niet. Een van de installaties is uitgekleed tot de fundamenten, om elders de Euro 7-accreditaties te ontvangen.
Non-uitlaatemissies
Die Euro 7-norm heeft namelijk een belangrijke primeur ten opzichte van de voorgaande normeringen: voor het eerst zijn niet alleen de uitlaatemissies bron van zorg, maar ook die van de remmen, banden en ophanging afkomen. Deze niet-uitlaatemissies zorgen voor grofweg twee kampen bij de autofabrikanten en hun toeleveranciers. Allereerst zijn er die inzetten op het voorkomen/verminderen van emissies, maar er is ook een groep die de emissies wil afvangen om zo te voorkomen dat ze in het milieu belanden.
Een alles overkoepelende aanpak is lastig, vertelt Andreas Mayer. “Bij sommige toepassingen kun je de remmen al aan de Euro 7-normen laten voldoen door relatief simpele ingrepen. In Amerika kijkt men vooral naar schoonblijvende wielen en is remstof om die reden al decennia een onderwerp. Die lessen helpen nu. Tegelijkertijd moet wel voldaan worden aan die andere eisen zoals het voorkomen van trillingen en bijgeluiden die niet in alle markten even sterk spelen maar hier in Europa wel. Zodra voertuigen krachtiger worden, zwaarder wegen en een hoger zwaartepunt krijgen wordt het steeds lastiger om zonder al te grote ingrepen te kunnen voldoen aan de nieuwe norm. De opkomst van gecoate schijven is een ontwikkeling die is toe te schrijven aan Euro 7, net als de terugkeer van de trommelrem. Dit is een gesloten systeem en daarmee minder gevoelig voor het uitstoten van dergelijke emissies. Op de achteras uiteraard, want de vooras blijft het domein van de schijfrem.”