Vraag iemand naar mogelijke innovaties bij lakleveranciers en tot de antwoorden behoren al gauw nieuwe kleuren of zelfhelende eigenschappen, misschien zelfs kleurverandering (denk aan BMW iX Flow). Weinigen zullen denken aan brandwerende coating in een accupakket.
Een autobrand is een ingrijpende gebeurtenis, bij elke auto. Een benzine of diesel brandt een uurtje en is dan uitgeblust. Een elektrische auto brandt een week en verlangt het equivalent van twintig brandweerauto’s om uit te krijgen. We kennen de beelden van EV’s die in een levensgroot aquarium worden gedropt om er veilig te kunnen blijven smeulen. Dat er hierna sprake is van het nodige chemisch afval moge duidelijk zijn.
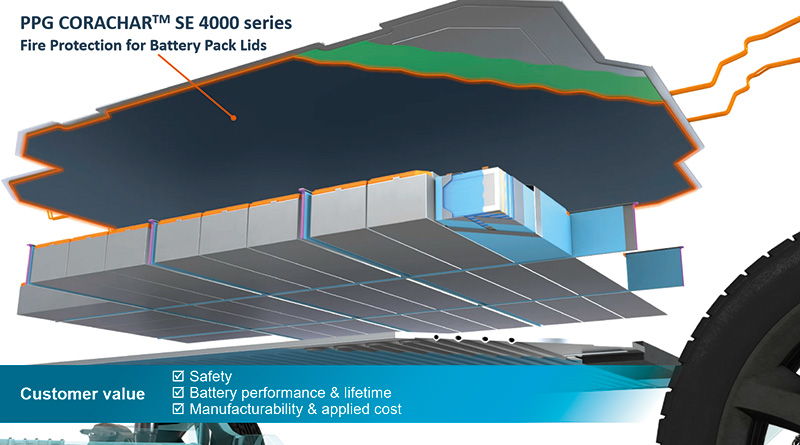
Fabrikanten en toeleveranciers steken veel energie in het voorkomen en beperken van dergelijke tragedies. Ook lakfabrikanten. PPG, goed voor een wereldwijde omzet van bijna 16 miljard euro, verzamelde de internationale pers op de productie- en researchfaciliteit in Amsterdam voor een inzage in de kunde op velerlei terrein. Want de automotive is maar één pijler onder het bedrijf, net als luchtvaart, scheepvaart, de bouw en de verpakkingsindustrie dat zijn. Dat blikje fris of die deo-spuitbus kan dus maar zo een PPG-afwerking hebben gekregen. Een ander voorbeeld zijn de UV-werende ruiten in vliegtuigen en de bijzonder zuinige organische materialen voor OLED-toepassingen zoals smartphones of de schermen in auto’s.
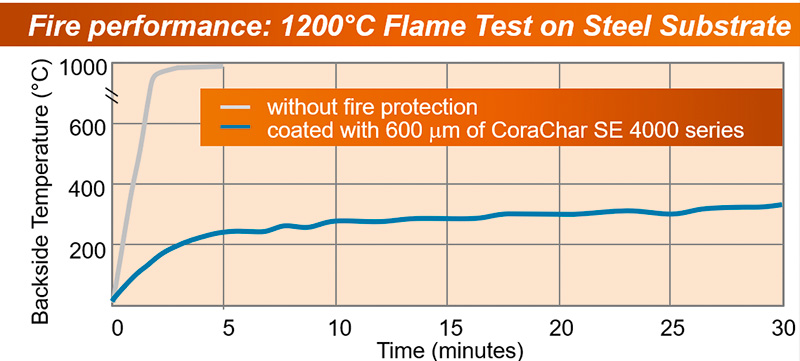
300 jaar in 3 minuten
De keuze voor Amsterdam onderstreept de lange band van PPG met ons land. Jan Pieterszoon Schoen, voorouder van de bekende ondernemer en investeerder Pieter Schoen, bouwde in 1722 in Westzaan een windmolen om pigmenten te malen. 250 jaar later volgt een fusie met twee collega’s tot Sigma Coatings, dat in 2008 weer door PPG werd overgenomen. PPG zelf kwam overigens ‘pas’ in 1883 tot leven. Veel tijd om stil te staan bij het verleden hebben we echter niet. In het museum waar we staan gaat het al snel over de moderne elektrische voertuigen en het accupakket.
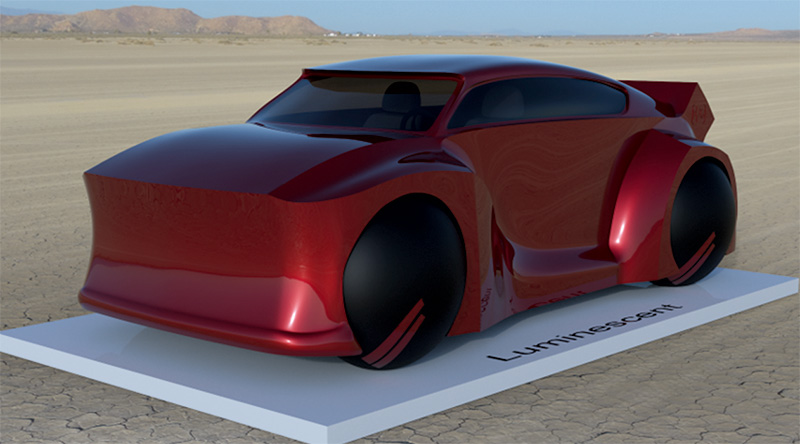
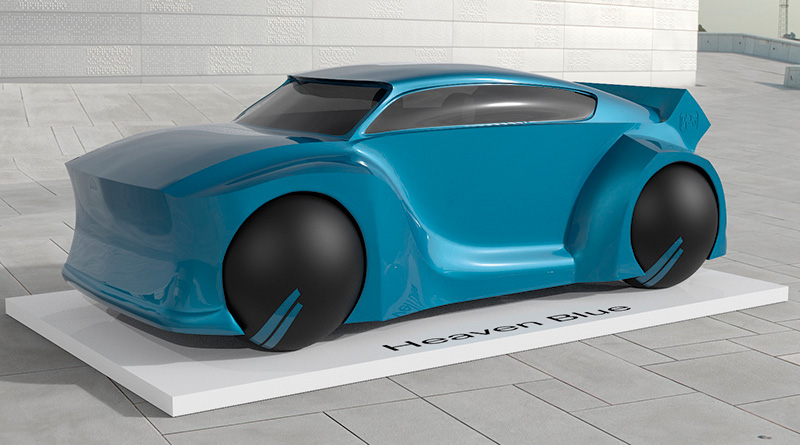
William Brunat geeft als directeur productontwikkeling inzage in de marktkansen buiten de zichtbare lakken op een auto. Twee productlijnen krijgen van hem het podium: de di-elektrische coatings en de coatings die elektrische voertuigen beschermen tegen brand. Beide komen voor in het accupakket. Om te beginnen met de laatste, de brandwerende coating: die is bestand tegen temperaturen tot 1200 graden Celsius. Bovendien verlaagt het de achterliggende temperatuur naar maximaal 400 graden.
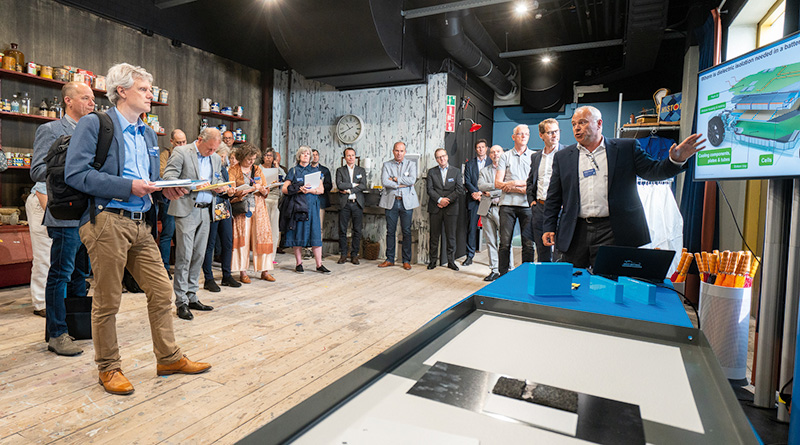
De di-elektrische coating biedt een fundamentele isolerende werking. Waar menig elektrische auto momenteel werkt met 400-600 volt loopt dat bij nieuwe modellen hard op naar 800 of zelfs 1000 volt. Isolatie die kortsluiting moet voorkomen wordt doorgaans opgelost met folie of tape, maar dan zijn er risico’s zoals luchtbellen of naden. Ook is er de relatief complexe en bewerkelijke methode van het aanbrengen. Dit in tegenstelling tot de te spuiten coatings. Behalve een toegenomen veiligheid, roemt Brunat ook de andere producteigenschappen zoals het tegengaan van bekende problemen die de levensduur van zo’n pakket kunnen beperken.
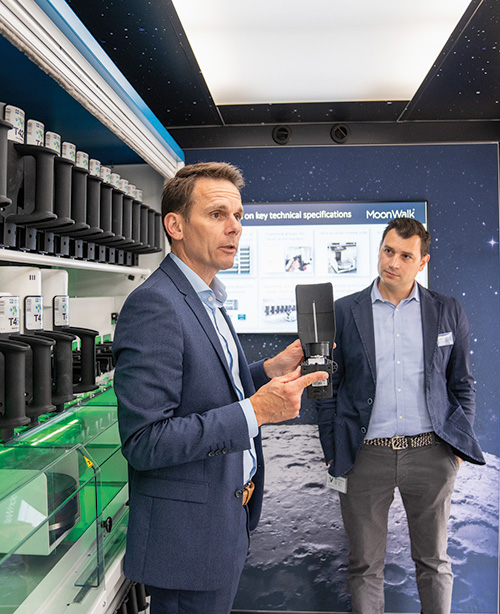
Duizend maal Moonwalk
Moonwalk, de geautomatiseerde mengkamer van PPG, begint in de Benelux al een bekende te worden. Het systeem telt tachtig opbergplekken voor pigmenten en dertien actieve posities. Bij het instellen van de Moonwalk geeft deze zelf aan welk pigment op welke actieve positie moet komen. Als een pigment er nog niet aanwezig is, dan moet deze wel even met de hand worden aangebracht. Daarna neemt de machine het mengproces verder over. Met zo’n duizend geïnstalleerde units is het beeld duidelijk: steeds meer klanten zien de voordelen van een automatisch mengsysteem dat tijd bespaart en de precisie verhoogt. De nauwkeurig afgewogen pigmentbestanddelen zorgen ervoor dat de resulterende lak altijd hetzelfde is. “Het is gebruikelijk om wat meer lak te mengen dan strikt noodzakelijk om eventueel kleurverschil te voorkomen als er achteraf moet worden bijgemengd. Met Moonwalk voorkom je verspilling. Bovendien kun je de machine laten mengen en ondertussen andere taken verrichten. Om nog maar te zwijgen van de veel schonere werkomgeving. In een traditionele mengkamer zijn de sporen van eerdere sessies duidelijk zichtbaar.”
Jo de Wachter, new business manager Automotive Refinish Coatings, laat een cruciaal element zien van de Moonwalk achter hem. Hiermee vindt de lak in de flacon automatisch en nauwkeurig afgewogen de weg naar de mengbeker eronder. Matteo Carraro (Moonwalk segmentmanager EMEA) kijkt toe.